Cuáles son y cómo se pueden prevenir
10 errores que impactan en la seguridad en áreas logísticas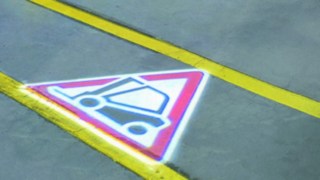
En el sector de la logística y la manipulación de mercancías se producen al año más de 50.000 accidentes. Aunque en los últimos años este número se ha visto reducido, aún queda mucho trabajo por hacer en cuanto a seguridad preventiva. Los errores que se pueden encontrar en estos espacios logísticos son comunes en las diferentes aplicaciones. Sin embargo, en muchas ocasiones estos accidentes pueden ser prevenidos de forma fácil y sencilla.
Una mala práctica puede resultar en grandes costes para la compañía, no sólo económicos (coste de reparación/sustitución maquinaria, mercancía dañada, reparación de instalaciones, bajas laborales del personal, posibles denuncias, multas o penalizaciones derivadas de inspecciones, paro de la actividad, recuperación de la producción perdida o tiempo empleado de los mandos intermedios y elevados en el análisis y resolución de esos accidentes son sólo algunos de ellos), si no también costes humanos (lesiones o, en el peor de los casos, fatalidades).
Por otro lado, se debe tener en cuenta que, tras un accidente, el índice productivo sufre una bajada ya que los empleados pierden la confianza en la compañía. Esto se puede llegar a retomar, pero es necesario tomar medidas preventivas para no llegar a ello.
¿Cuáles son los errores en las áreas logísticas y de almacén? Identificamos los 10 más comunes
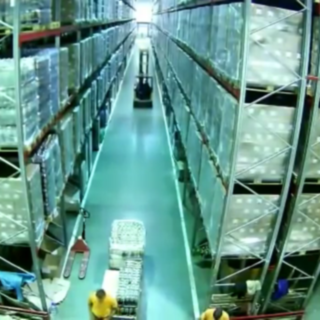
1. Conductores no formados
Muchas veces, cuando ponemos un vehículo en manos de personal inexperto estamos multiplicando las probabilidades de accidentes en nuestro entorno logístico. Sin embargo, estas probabilidades también pueden ser elevadas si el personal no posee formación específica en el vehículo que manipula. Por ello, se debe tener en consideración el conocimiento que dicha persona posee para el manejo de un vehículo en concreto, pues puede suceder que el personal posea el certificado de carretillero, pero haya realizado la formación con un vehículo completamente diferente.
CONSEJO:
Debemos tener en cuenta la normativa UNE58451 que estructura la formación de carretilleros en dos categorías diferentes de vehículos:
Cat 1. Apiladores, transpaletas y recogepedidos. Hace referencia a conductores acompañantes o subidos a plataforma.
Cat. 2. Carretillas contrapesadas, Retráctiles y de Pasillo estrecho.
En ambos casos la formación debe ser de 24h en conductores noveles y de 8h en las formaciones de reciclaje cada 5 años (ambas incluyendo teoría y práctica).
Para facilitar la gestión de la flota y del personal autorizado para su conducción se puede obtener un sistema de gestión de flotas. ¿Cómo nos puede ayudar? Se pueden asignar a los conductores con sus respectivas carretillas.
Además, se pueden establecer límites de velocidad por carretilla, incluir alertas de renovaciones de formación o de chequeos médicos anuales, y realizar informes de impactos en cada uno de los vehículos.
2. Golpes a Estanterías | Infraestructuras / Cargas
Los golpes a estanterías y otras infraestructuras son uno de los accidentes más comunes que podemos encontrar en los almacenes. Aunque la gravedad de los mismos puede variar, es importante su prevención.
Existen empresas certificadas que pueden realizar la reparación de estanterías dañadas. Además, éstas se deben proteger con protecciones metálicas o de absorción de impactos.
CONSEJO:
Aunque el coste de este último tipo de protección es más elevado, a la larga tienen una mayor vida útil, no necesitan reparación y no causarán daños ni a las instalaciones ni a las carretillas.
Sin embargo, siempre se deben analizar todas las opciones y ventajas de cada una de ellas en sus diferentes aplicaciones.
Si pensamos en vehículos, existen sistemas de detectores de obstáculos además del ya mencionado sistema de gestión de vehículos para el control de la velocidad de éstos. En el caso de los vehículos que operan a grandes alturas, se deben tener en consideración los estabilizadores de carga para así evitar pandeos en la translación de la mercancía a grandes alturas y, por ende, posibles accidentes y golpes a las estanterías y mástil de la carretilla.
Por último, un elemento tan sencillo como la instalación de señalizaciones de circulación puede facilitar la conducción de los carretilleros ya que frecuentemente se guían por referencias dentro del espacio logístico.
3. Mala manipulación de cargas
Un simple despiste, falta de concentración, inexperiencia o ir con prisas puede generar un accidente y la pérdida de la carga manipulada. ¿Qué se puede hacer?
Una vez más, se debe prevenir. Para ello existe una gran variedad de elementos que se pueden incorporar a la carretilla y que favorecerá la reducción de incidencias. Algunos de ellos son:
- Rejas de carga en las horquillas que mantendrá la carga estable durante su manipulación y translación.
- Tejadillos: todos los vehículos con una elevación por encima de 1800 milímetros deben llevar tejadillo (FOPS). Existen diferentes tipologías de tejadillos (metacrilato, rejas, cristales, etc.) que se deben de tener en cuenta a la hora de configurar un vehículo, para adaptarse a la carga manipulada.
4. Marcha adelante sin visibilidad
Idealmente se debería evitar a toda costa este tipo de circulación, sin embargo, en ocasiones no es posible debido a la configuración de las instalaciones. La normativa establece que, en caso de no disponer de visibilidad frontal, el carretillero debe realizar la conducción marcha atrás. Para favorecer esta visibilidad, cada proveedor de maquinaria posee sistemas auxiliares de asistencia que pueden facilitarla en diferente medida.
CONSEJO:
Se recomienda disponer de asientos giratorios cuando los desplazamientos marchan atrás son muy habituales y de largas distancias. Esto evitará sobreesfuerzos musculoesqueléticos en el personal.
También es posible incorporar cámaras de visión trasera para facilitar la conducción y seguridad del entorno. Si no se desea disponer de pantallas en las carretillas, se pueden incorporar sistemas de detección de peatones que alerten al conductor y los peatones.
5. y 6. Falta de control de uso de cinturón + velocidad inadecuada
Generalmente, una de las principales causas de fatalidades que podemos encontrar en el sector logístico es la combinación de una falta de uso del cinturón de seguridad y una velocidad inadecuada.
La normativa requiere poseer de un sistema de retención que puede ser el cinturón, puertas de cabina o de retención con enrejado. El cinturón de seguridad, aunque no es obligatorio su uso en todos los tipos de carretillas como las retráctiles, es un elemento de seguridad pasivo fundamental. Si bien puede parecer un elemento ‘molesto’ para algunos conductores que deben subir y bajar de la carretilla con cierta frecuencia, su uso preverá posibles fatalidades en caso de accidente.
Otros elementos de seguridad pasiva son incluidos ya de serie en las carretillas por normativa.
Por otro lado, se debe intentar que la carretilla posea un sistema de seguridad activa que analice la velocidad y el ángulo de giro del vehículo y realice una reducción automática de la velocidad.
Como se ha mencionado con anterioridad, existen sistemas para la limitación de la velocidad de los vehículos y que pueden ser combinados con sistemas de limitación de velocidad por zonas o sistemas auxiliares de asistencia a la conducción. La elección de uno u otro dependerá de las necesidades de cada compañía y la flota que posea.
7. y 8. Falta de visión en cruces | Golpes entre carretillas
Muchas veces un mal uso de las carretillas o despistes en la conducción puede resultar en accidente. La probabilidad de que esto suceda en cruces o intersecciones es mucho mayor ya que la visibilidad no suele ser la más adecuada.
Existen elementos pasivos que pueden ser instalados en los cruces como los espejos panorámicos o la señalización visual de la aproximación de vehículos.
Si revisamos algunos de los elementos activos más comunes encontramos sistemas de aproximación de carretillas que indicará cuando dos, o más, carretillas se encuentran a una distancia de proximidad establecida. Este sistema varía de proveedor en proveedor por lo que se debe evaluar todas las opciones posibles.
9. y 10. Desorden general en las instalaciones | Pavimentos en mal estado
A la hora de evaluar un posible accidente dentro de las instalaciones se deben tener en cuenta todos los factores que pueden tener un efecto en el mismo. Factores como los anteriormente mencionados por sí solos pueden no resultar en accidente. Sin embargo, hay dos elementos claves que se deben tener en consideración: el desorden y los pavimentos en mal estado.
El orden dentro de los espacios logísticos y productivos es básico. No sólo para la prevención de accidentes, sino también para el aumento de la productividad. Un espacio de almacenaje ordenado y catalogado con la correcta identificación de las diferentes zonas puede suponer un aumento de la productividad en un 5%, ya que el personal sabrá identificar con mayor facilidad y en un menor tiempo dónde ubicar/cargar la mercancía. Por ende, esta reducción de tiempo también se puede ver reflejada en una reducción de los costes.
El pavimento de las instalaciones suele ser un elemento olvidado en la gestión de un almacén. En algunos casos se antepone la estética a la funcionalidad, mientras que en otros casos no se tiene en cuenta. La correcta elección y mantenimiento del pavimento tendrá un efecto directo en la elección de la flota de carretillas y los sistemas de seguridad adicionales que deberemos adquirir para contrarrestar las irregularidades del suelo y así prevenir posibles accidentes.
En definitiva, a parte de la concienciación del personal, un correcto análisis del espacio logístico y de almacenaje es básico para la prevención de accidentes.
El cómo prevenirlos y con qué medios debe responder a las características y necesidades del espacio, el personal y la compañía. Y, por supuesto, en caso de duda consultar a tu proveedor o empresa que ofrezca un servicio de consultoría de seguridad integral.