Factores de riesgo en instalaciones y tendencias para un tráfico interno seguro
Tendencias seguras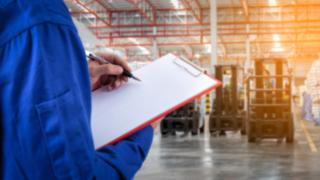
Por Marc Castro, Safety Product Manager en Linde Material Handling Ibérica, para 'Tribuna CEL'
Los accidentes en el tráfico interno siguen implicando un factor de riesgo para personas, mercancías e infraestructuras en el almacén y todavía el sector tiende a invertir en seguridad después de un accidente, lo que se traduce en costes derivados evitables. Analizamos los factores que intervienen en ese riesgo y las tendencias seguras para contribuir a crear un ecosistema confiable, rentable y productivo.
El riesgo de trabajar en un entorno industrial y, particularmente logístico, conviviendo con herramientas, soluciones y sistemas de almacenaje y manutención como carretillas elevadoras y otros equipos, sigue siendo importante, pero colocarlo como uno de los principales aspectos a tener en cuenta para el desarrollo de los negocios aún es un reto.
Durante 2020 y hasta el mes de agosto se han registrado un total de 194 accidentes graves en el ecosistema intralogístico. Así lo confirman datos arrojados por el Ministerio de Trabajo al tiempo que se remarca que, en concreto estas cifras, se corresponden con zonas de almacenamiento, carga y descarga, contabilizando hasta 32 fallecimientos.
Añadir que, si hiciéramos una extrapolación a los 12 meses, nos darían unas cifras, aproximadas de casi 40.000 accidentes, con 318 graves y 75 fallecidos. La cifra es alentadora, pero hay que tener en cuenta que muchas empresas estuvieron cerradas durante un largo periodo.
Nota: Los valores reflejados correspondientes a 2020 son un cálculo aproximado tras la extrapolación de los valores de enero a agosto 2020 ofrecidos por el Ministerio de Trabajo y Economía Social.
Fuente: Ministerio de Trabajo y Economía Social. (2016 – 2020) Informe ‘Estadísticas de Accidentes de Trabajo’. Consultado en: http://www.mites.gob.es/estadisticas/eat/welcome.htm
Con un panorama como el descrito, no cabe otra posibilidad que no sea la de buscar los factores que lo están desencadenando y dar con la palanca de cambio que nos lleve a generar ecosistemas más seguros y confiables para personas, mercancías e infraestructuras.
Factores de riesgo que desembocan en accidentes en el almacén
Son numerosos los motivos por los que se generan incidencias dentro de las instalaciones logísticas de las empresas y muchos de ellos no son necesariamente fallos internos, sino también externos. Sin embargo, sí podemos acotar en tres factores los más acusados:
- Formación insuficiente:
La profesión logística se está dignificando cada vez a mayor velocidad y esto también está implicando una mejora en términos de capacitación, pero todavía nos enfrentamos a sectores industriales que marcan en el segundo plano la formación de sus empleados y mozos de almacén, en términos de seguridad y ergonomía.
El incremento de la formación pasa, entre otras cosas, por generar un cambio de mentalidad con el que se generen nuevos hábitos en la industria y eso se traduzca en designar un mayor valor y responsabilidad en los puestos operativos, que están realmente en manos de quienes está la productividad y la evolución de los negocios.
Invertir en formar a las personas que realmente realizan el trabajo es un seguro de vida para ellos y para el desarrollo de la actividad, y no hacerlo conlleva una falta de conocimiento e información que tienen graves consecuencias, pero podrían resolverse en poco tiempo y con pocos recursos.
- Rotación de personal:
Muy ligado a lo anterior y con un enfoque de talento y profesión, el hecho de tener una alta rotación de personal implica muchas veces el descuido, por parte de los decisores, de la implementación de las medidas de seguridad adecuadas para un entorno como el intralogístico.
De hecho, los picos de demanda como las grandes campañas navideñas o de eCommerce comportan contrataciones adicionales por cortos periodos y que luego no necesariamente implican una relación laboral duradera, lo que no motiva a las compañías a invertir en formación o información en términos de seguridad para sus empleados.
- Falta de inversión:
Todavía tendemos a resolver el problema en lugar de a prevenirlo y normalmente se toman decisiones de inversión cuando el accidente ya ha ocurrido, lo que supone un tremendo error.
La seguridad tiene que ser lo primero en cualquier instalación y si eso supone realizar mejoras o añadir elementos que contribuyan a ello, esa inversión tendrá un claro retorno desde todo punto de vista.
De nuevo, ha de llegar un cambio de mentalidad para invertir en sistemas de seguridad, sobre todo, con respecto a herramientas y equipos para la instalación.
Tendencias seguras: hacia dónde vamos y algunos consejos
Por otro lado, y mirándolo desde una óptica más positiva, las posiciones de control e implementación de medidas van en aumento, así como los servicios de consultoría especializados en aspectos concretos como carretillas, circulación de peatones o riesgos específicos (control de químicos, gestión de stock, señalización de conductos...etc).
- Ergonomía:
La ergonomía y confortabilidad del operario siguen siendo dos factores que son revisados con regularidad por las empresas ya que no sólo se logra mejorar la operatividad de la actividad, sino que esto tiene un impacto directo sobre la seguridad en las instalaciones.
La comodidad del empleado favorece sustancialmente sus capacidades en el puesto de trabajo y ayuda a que trabaje en un entorno seguro y sencillo. De hecho, cada vez son más las herramientas de trabajo que se adaptan al operario y a la aplicación en cuestión, desde la lectura de códigos con láser en dedo, hasta las gafas virtuales.
Por otro lado, cabe destacar que, aunque la automatización siga aportando un valor especial en procesos, mejorando y optimizándolos, el factor humano seguirá estando presente, por lo que fijar medidas de seguridad alineadas con su ergonomía es clave ahora y en el futuro.
- Big Data:
No es noticia que los datos lo son todo hoy en día y que sin ellos no podemos visibilizar las operativas, registrar patrones de comportamiento y tomar decisiones. Por ello, el Big Data no deja de ser, directa e indirectamente, una valiosa herramienta de seguridad.
Se realizan inversiones, ventas y mejoras de procesos gracias a esta metodología y en términos de seguridad tampoco se queda atrás.
Es crucial analizar lo que ha ocurrido durante y tras un accidente, recoger los factores de riesgo y basarse en eso para tomar decisiones de inversión futuras con el objetivo de que estas den el máximo rendimiento.
Las empresas buscan cada vez más poder tener un buen registro de sus empleados, desde los KPI’s en algunas posiciones, hasta las horas que han estado utilizando cierta máquina/vehículo. Esto es posible gracias a la gestión telemática de estas herramientas de trabajo.
Si después de leer esto te preguntas: ¿hacemos un buen análisis de los datos que podemos obtener? Bien. Pues esta pregunta la resolveremos en otra ocasión como elemento esencial en el tratamiento de la información masiva.
- Costes asociados:
No hay que olvidar el apartado financiero. Los costes derivados de los accidentes en el tráfico interno suelen doblar los costes de inversión en prevenirlos, por lo que seguimos insistiendo en lo crucial que es prevenir para evitar costes innecesarios.
Mi recomendación para los técnicos de PRL y diferentes responsables, es que cuando realicen un estudio de incidente o accidente, incluyan los costes asociados a dicha situación, como: personal implicado y tiempo de paro, reparación de bienes, reparación de infraestructuras, personal de mando y tiempo invertido para analizar y resolver la situación, recuperación de la producción perdida, así como las compensaciones a clientes por falta de entregas.
A pesar de todo esto, desafortunadamente seguiremos sin poder contabilizar otros factores tales como la bajada del rendimiento del personal o el daño que se genera a la imagen de la empresa.
Soluciones con buen resultado
Desde Linde Material Handling Ibérica hemos podido comprobar en distintas industrias cómo funcionan algunas tecnologías aplicadas a evitar incidencias de seguridad y que, además ofrecen un buen resultado.
- La gestión de flotas: aplicable tanto para vehículos de manutención que circulan por vía pública, como los que trabajan dentro de instalaciones, nos permiten ver al detalle ubicaciones, tiempos de trabajo o de paro, con el fin de optimizar procesos y flotas.
- Sistemas de detección de obstáculos (muy implementado ya en el sector de la automoción) y peatones mediante visión directa con cámaras capaces de distinguir personas y obstáculos, o mediante sistemas de radio frecuencia para detectar dónde están las personas, evitando atropellos y ayudando a mantener distancias seguras o evitar colisiones entre vehículos.
- Barreras inteligentes que impiden el paso de peatones cuando hay vehículos en las proximidades de la instalación.
- Iluminación de advertencia instaladas en los propios vehículos, para avisar de aproximación, o ubicadas en puntos estratégicos de pasos peatonales, que se activan al encontrarse un vehículo en las inmediaciones.
- Protecciones absorbentes de impactos que reducen los daños ocasionados tanto al elemento que golpea, como al que recibe el impacto.
- Señalización vial para la gestión del tráfico, como si de la vía pública se tratara: líneas de separación de carriles, implementación de semáforos…etc.
- Dejarse asesorar por expertos, cuando alguien sabe de un tema, a veces la mejor opción es escucharlo. Muchas consultorías se han especializado en riesgos específicos que los técnicos de prevención actuales no disponen del tiempo necesario para especializarse.
La variedad es tan amplia como las necesidades que se plantean, pero al final todos buscamos lo mismo: mejorar la ergonomía y la seguridad, con el fin de aumentar la productividad.