Heidelberger Druckmaschinen AG
Un soplo de aire fresco en la logística de Heidelberg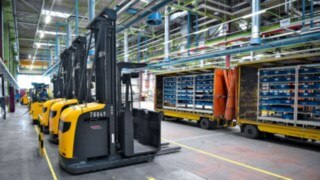
En unos tiempos de requisitos cada vez más personalizados por parte de los clientes, también la intralogística debe adaptarse gradualmente a las condiciones de producción cambiantes. El ejemplo de Heidelberger Druckmaschinen AG en Wiesloch/Walldorf (Heidelberg, Alemania) muestra cómo puede afrontarse este reto en una empresa industrial global. En colaboración con Linde Material Handling y su socio contractual Suffel Fördertechnik como contratista general, allí se ha puesto en pie un concepto logístico totalmente nuevo que optimiza el suministro de material a las líneas de montaje de máquinas de impresión offset.
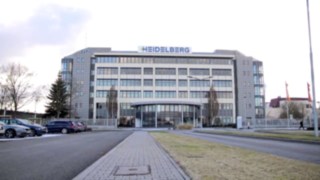
El colorido envase de cereales en la mesa del desayuno, la lujosa revista satinada durante la pausa para el café o la elegante tarjeta de visita durante el almuerzo de negocios: pese a la creciente digitalización de nuestro mundo moderno, seguimos entrando constantemente en contacto con productos o materiales impresos. Y por muy diferentes que estos puedan ser, es bastante probable que hayan sido producidos en una Speedmaster de Heidelberg. No en vano, la empresa mundialmente conocida es, con 11.500 empleados, uno de los líderes del sector. Este especialista en impresión tiene su sede central en Wiesloch/Walldorf, Baden-Württemberg, en el corazón de la económicamente pujante región metropolitana alemana Rhein-Neckar, donde se cruzan las transitadas rutas de tráfico de norte a sur A5 y A6. Es aquí donde Heidelberg opera la mayor y más avanzada fábrica de máquinas de impresión del mundo: en una superficie de un kilómetro cuadrado se producen en las más diversas clases de formato, las máquinas de impresión offset líderes del mercado.
New challenges –
New Concepts
Heidelberg has been observing a steady change towards greater individuality in the area of customer requirements for a number of years: "Previously, we predominantly built similar printing machines at each site," remembers the Head of Plant Logistics Matthias Ehmler. "Now, we frequently manufacture customized systems and because of this, there has been a sharp rise in the number of different versions," he explains.
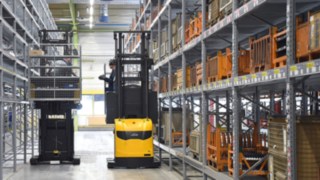
Linde reach trucks and order pickers in the Heidelberger Druckmaschinen warehouse
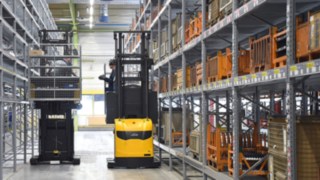
Linde reach trucks and order pickers in the Heidelberger Druckmaschinen warehouse
This customizing trend ultimately also affects the assembly lines: "Workers at the assembly stations were increasingly moving between unmanageable 'material mountains'. The greater the variety, the more parts containers were required. This had an increasingly negative impact on employee productivity," Ehmler explains. "As a result, two years ago, we launched a project to reorganize the assembly department. We wanted to use the production areas more efficiently and bring the material to the worker, not the other way around."
The restructuring of the assembly department towards a modular construction included a reorganization of the intralogistics in the 600-meter-long hall. In future, materials with low daily requirements will no longer be provided in containers on site, rather they will be ordered and picked on kit carts and introduced to the assembly lines by load trains. A central order picking and consolidation area with high racks was set up at the front end of the assembly hall for this purpose. Upstream buffer zones were specified as interfaces for the internal transport systems and as transfer stations for the kit carts.
"Our aim was to ensure a safe, efficient and flexible material supply with the best possible use of the available space," explains the Head of Heidelberger Factory Logistics. An ambitious project, whose implementation during ongoing operation required the perfect meshing of all the different cogs.
Se busca socio competente
Los responsables pasaron a la fase de licitación con un extenso pliego de condiciones. «Buscábamos un socio capaz de implementar como contratista general la construcción de estanterías y la dotación con vehículos de manutención, incluida la gestión de la flota. Al mismo tiempo, naturalmente, debían cumplirse el calendario y el presupuesto fijos acordados con nosotros, de modo que pudiéramos concentrarnos plenamente en la gestión de los datos básicos y la formación de los empleados», esboza Ehmler la tarea planteada a las empresas logísticas concursantes. La decisión de adjudicar el contrato al fabricante y proveedor de soluciones Linde Material Handling junto con su socio contractual Suffel Fördertechnik obedeció a diversos motivos: «Por un lado, los equipos de Linde nos impresionaron con sus características técnicas distintivas, tales como los remolques de carros con barras para el tren de remolques o el preparador de pedidos de gran altura. Por otro lado, nos convencieron tanto el asesoramiento como, naturalmente, las condiciones contractuales», explica Ehmler.
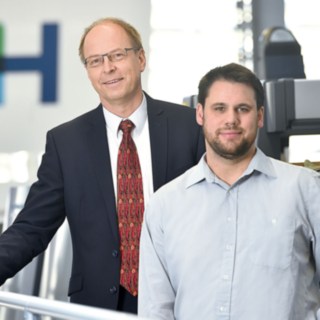
«Encargar a un mismo proveedor la construcción de estanterías y los vehículos de manutención se reveló como un acierto en todos los sentidos».
Matthias Ehmler, director de Logística de planta
A fin de posibilitar la puesta a disposición de las piezas en las líneas de montaje de manera específica para cada encargo, en primer lugar había que hallar una solución adecuada para el almacén de preparación de pedidos y, por ende, el elemento central del nuevo concepto logístico: «Ya habíamos plasmado ideas y especificaciones concretas en el pliego de condiciones. Una vez adjudicado el contrato, se fueron refinando gradualmente con Linde y Suffel. El almacén de preparación de pedidos debía permitir el almacenamiento de piezas grandes y pequeñas, así como de grupos constructivos enteros, posibilitar distintas geometrías de contenedor y, al mismo tiempo, satisfacer los elevados estándares de protección laboral», resume los principales retos el Director de proyectos Stefan Heger.
Un supermercado bien surtido
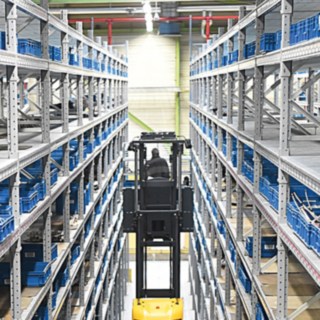
El nuevo almacén de estanterías altas, con 13 filas de estanterías y 4.500 referencias de artículos, actúa como supermercado y consta de una zona de pasillo ancho con un ancho de pasillo de 4,05 metros y una zona de pasillo estrecho con tres pasillos. En el pasillo ancho, tres carretillas retráctiles del modelo Linde R14 se encargan de almacenar el material, mientras que en el pasillo estrecho los siete preparadores de pedidos de gran altura Linde V modular ejecutan tareas de preparación de pedidos y reponen suministros. El almacén se abastece desde tres fuentes distintas: las unidades de carga grandes acceden al área de preparación de pedidos a través de un puente de conexión desde el almacén de suministro central directamente adyacente. Las unidades de carga pequeñas se preparan previamente en un almacén de piezas pequeñas automático y se suministran mediante el sistema de transporte interno. Las compleciones se llevan a cabo en función de las necesidades en el área de premontaje conectada al área de preparación de pedidos.
La ergonomía y la seguridad desempeñan un papel clave
Para la preparación de pedidos en la estantería de alto nivel se utilizan exclusivamente preparadores de pedidos de gran altura Linde V modular. Desde el vehículo, los empleados retiran el material requerido a una altura de hasta 6,50 metros y lo cargan en los carros de kit de enrejado metálico de aproximadamente 1,80 metros de altura.
y 1,60 metros de anchura, capaces de soportar un peso máximo de 500 kilogramos. Se depositan hasta tres pedidos en un carro de kit. Para que los empleados puedan acceder fácilmente al compartimento de la estantería, los preparadores de pedidos de gran altura incorporan barreras inclinables integradas. «Esta opción de equipamiento es una verdadera característica distintiva de Linde, a la cual podemos sacarle el máximo partido en nuestra nueva estantería de alto nivel», enfatiza Jens Kernbach, Director de Logística de nave de Heidelberg. «No en vano, también en Heidelberg notamos los efectos del cambio demográfico y tenemos una responsabilidad para con nuestros empleados».
A fin de garantizar que la preparación de pedidos transcurra literalmente sin fricción, los equipos que se mueven por los pasillos de estanterías están guiados por inducción. Esto permite al operador concentrarse plenamente en el proceso de preparación del pedido mientras circula a una distancia óptima respecto de la estantería. El equipamiento del vehículo incluye también un asistente de seguridad en el pasillo, que en caso necesario frena el equipo de forma controlada hasta detenerlo. «Ahora podemos descartar daños a la estantería
o a los equipos», celebra el Director de proyectos Heger. Además se han asegurado las entradas al almacén mediante barreras fotoeléctricas, que emiten de inmediato una alarma en caso de que personas no autorizadas accedan al área, aprobada exclusivamente para vehículos. También está preinstalada en los vehículos la navegación de almacén semiautomática de Linde, que brinda potencial para futuras optimizaciones. No en vano, esta solución basada en RFID permite a los preparadores de pedidos de gran altura navegar por el pasillo de estanterías hasta la ubicación especificada siguiendo una trayectoria óptima, sin intervención alguna del operador.
«Gracias a la guía de carril inductiva podemos descartar daños a la estantería o a las carretillas preparadoras de pedidos de gran altura».
Stefan Heger, Director de proyectos
Suministro flexible y compacto mediante trenes de remolques
Un total de tres trenes de remolques –denominados «Load Trains» en Linde– transportan los carros de kit cargados desde la estación de transferencia hasta los empleados de la producción de las líneas de producción. Cada uno de ellos consta de un tractor de arrastre del modelo Linde P50 y uno o dos carros con barras provistos de dirección en todas las ruedas y labios de elevación anchos. Cada remolque posibilita el transporte simultáneo de dos carros de kit, que gracias a la ausencia de eje central se pueden posicionar y retirar por ambos lados. «Esto nos permite una planificación flexible de los trayectos», explica el Director de proyectos Stefan Heger. Otra ventaja reside en el poco espacio que ocupa el tren de remolques de Linde, que mantiene con precisión su trayectoria mientras circula por un carril de 2,20 metros de anchura.
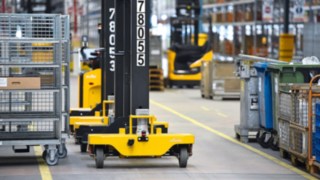
Balance positivo, pero la optimización continúa
Incluso una vez completada la inversión, el Director de Logística de la planta Ehmler sigue buscando nuevos potenciales de optimización. Uno de los elementos que considera más prometedores es el módulo «Análisis de utilización» de la solución de gestión de flotas de Linde. Ehmler lo explica así: «Llevamos ya muchos años utilizando “Connect:” para controlar el acceso a los vehículos y registrar impactos, y la experiencia con el sistema ha sido muy positiva. Ahora también podemos utilizar el software para optimizar nuestros procesos y, por ejemplo, mejorar aún más el grado de aprovechamiento de los equipos».
Hace ya casi un año desde que se implementó en Heidelberg la reestructuración de la intralogística basada en el almacén de estanterías altas, el preparador de pedidos de gran altura y el tren de remolques. Y la conclusión de Matthias Ehmler es decididamente positiva: «No solo implementamos el proyecto cumpliendo el calendario y el presupuesto previstos, sino que alcanzamos nuestro objetivo de racionalizar la logística. Linde y Suffel se han ganado en nuestro caso una referencia positiva».
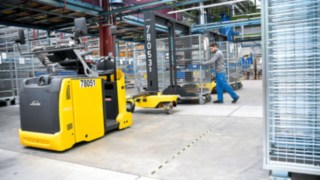